Penetrant Testing
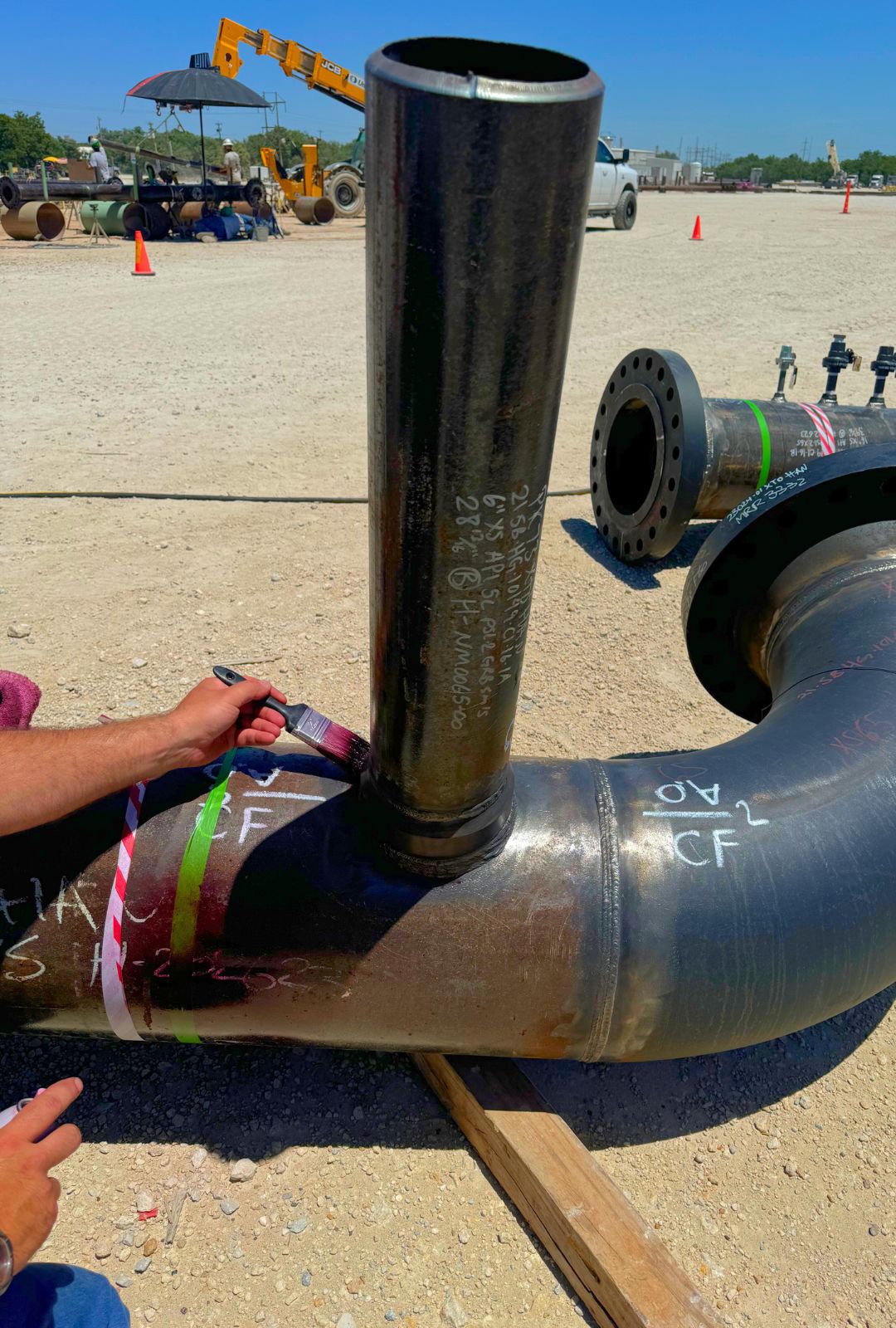
About IIAFS's
Penetrant Testing

Dye Penetrant testing plays a pivotal role in ensuring the structural integrity of essential equipment.

This non-destructive testing method is a simple, economical exam to give immediate results to any surface flaws.

This non-destructive inspection method begins by applying liquid penetrant to the cleaned surface of a component. The penetrant then soaks into surface-breaking defects such as cracks or porosity through a process called capillary action. After specified dwell time, the excess dye penetrant is removed. From here, a thin layer of developing agent is applied. The developer draws back the penetrant that remains in any defects in a process known as bleeding out. This bleed-out confirms any flaws on the surface of the part. This meticulous process detects even the most minute, minuscule flaws that could potentially compromise safety or lead to costly failures.
Our Approach
At IIAFS, dye penetrant testing goes beyond mere detection; once detection is made the investigation begins. Why is penetrant coming through? Why is it bleeding? Is there undercutting, a crack or just weld contouring? Thus, begins the process of understanding the root causes of the bleed-out and surface discontinuities in these components. Our process begins with meticulous surface preparation and the application of specialized penetrant materials that soaks into any potential defects. Once the materials are applied, skilled technicians carefully inspect the area to identify and categorize any indications of discontinuities. These findings are then analyzed to pinpoint underlying causes, whether they stem from welding defects, material flaws, or simply from outside, environmental factors. IIAFS’s thorough investigative approach not only ensures comprehensive defect detection but also provides valuable insights to address underlying issues proactively, enhancing the reliability and longevity of critical assets.
What is Penetrant Testing?
Dye Penetrant testing is a non-destructive inspection method used to detect defects in welds or castings. It works by applying a special liquid that seeps into any cracks or flaws. After the liquid is wiped away, a contrasting developing agent is applied. Any hidden defects become visible, helping ensure the integrity of critical equipment and structures.
Dye Penetrant Testing Methods
Visible Dye Penetrant Testing
Fluorescent Dye Penetrant Testing
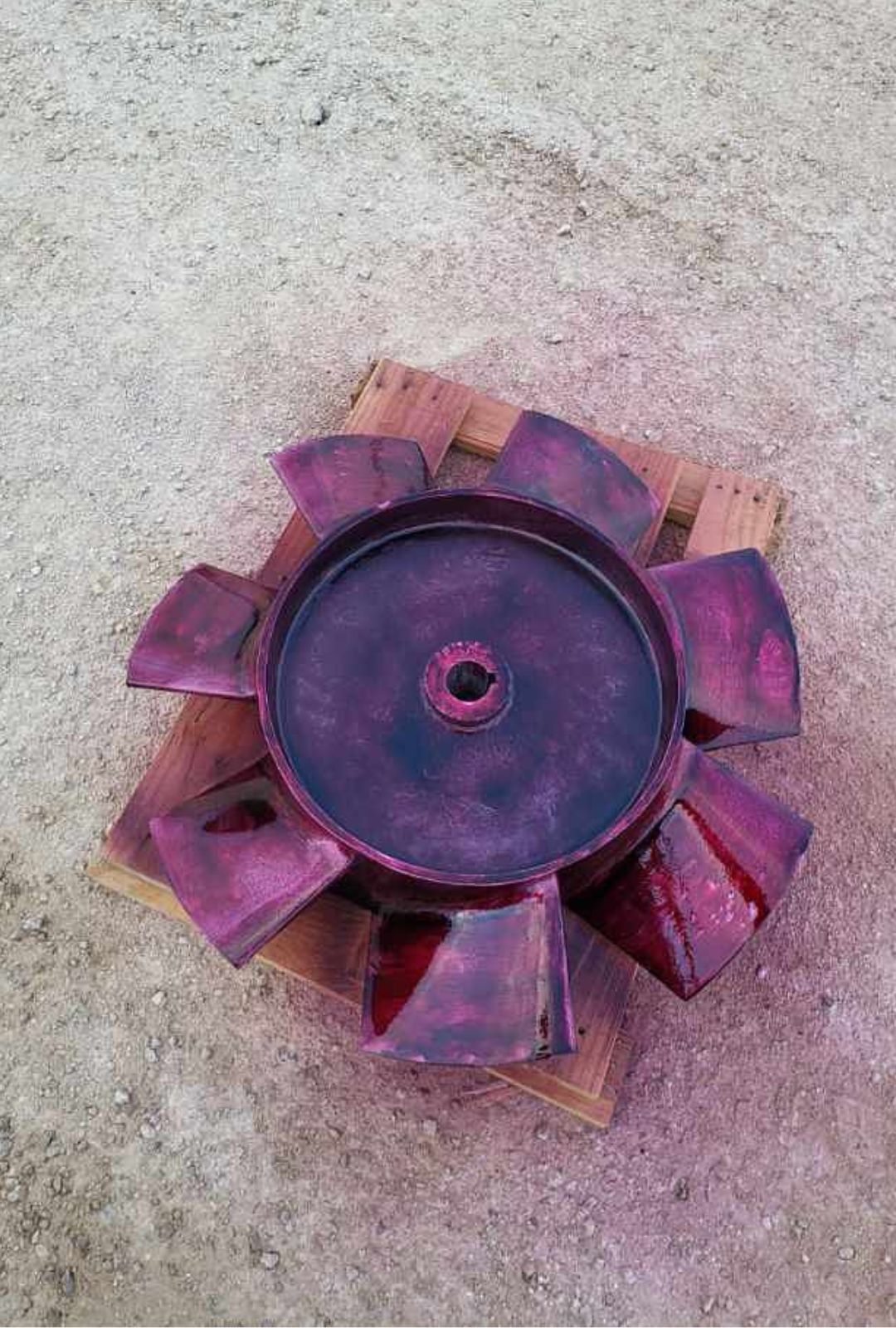
Benefits of
Penetrant Testing
Dye Penetrant Testing offers several key benefits in the oilfield.
- Reliable: Dye Penetrant Testing provides a reliable method for detecting surface defects such as cracks, porosity, undercut or incomplete fusion, ensuring the structural integrity of critical equipment and infrastructure.
- Cost-Effective: This proactive approach helps prevent costly downtime and mitigates the risk of catastrophic failures or leaks, thereby enhancing operational safety.
- Early Detection: Additionally, dye penetrant testing enables early identification of potential issues, allowing for timely repairs or replacements, which ultimately extends the lifespan of assets.
- Non-Destructive: Furthermore, its non-destructive nature means that inspections can be conducted without causing damage to the tested components, minimizing disruption to ongoing operations.
Why Choose Us?
We deliver results.
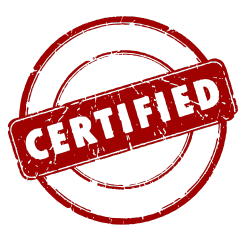
Ensure Equipment Integrity
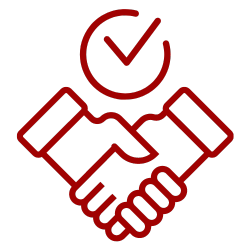
Highly Skilled Team
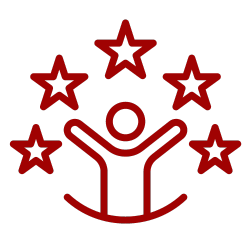
Commitment to Excellence
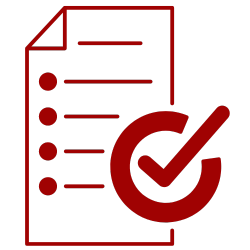
Regulatory Compliance
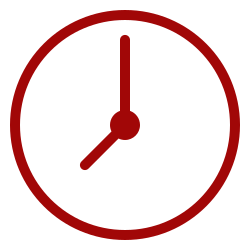
Long-Term Reliability
Industry Applications
Automotive
Manufacturing
Aerospace
Components
Parts
Manufacturing
Oil and Gas
Pipelines and
Pressure Vessels
Power Generation
Railroad
Infrastructure
Compressor
Stations
Contact Us
If you’re in need of reliable Non-Destructive Testing services for your welded or structural components, IIA Field Services is here to help. Get in touch with us today to learn more about our services or to schedule a consultation. We look forward to partnering with you to ensure the quality and integrity of all your oilfield products and components.